Have you lost faith in RPA deployment?
When it comes to automation, almost every business I have worked in or with has two things in common; firstly, they have all deployed Robotic Process Automation (RPA) to some degree. In some cases, this has been portfolio level deployment of hundreds or even thousands of bots, in others it’s been smaller scale deployments either as proof of concept or to tackle isolated issues. Secondly, the significant benefits these solutions delivered have been eroded over time.
This trend is something we at BFY hear a lot about from our clients. Companies that have saved hundreds of FTE through RPA deployments only to see these savings diminish over time as increased process fallout leads to recruitment having to refill these roles in subsequent years. For some organisations, this experience has led to scepticism regarding RPA and broader automation technologies.
In this article, we explore why automation value fades, and more importantly, how utilities can take practical steps to recover lost efficiencies and future-proof their RPA investments.
What is RPA used for?
Before we get into the reasons RPA can become less effective, let’s first look at how and why RPA is deployed in the first place. Most RPA strategies target high volume, low complexity processes. This allows for rapid solution development and maximum ROI. Back office areas within utilities typically employ significant resource behind the scenes. They handle customer queries, front line hand offs and system-generated exceptions. Processing these cases typically involves four key stages:

1) Trigger to Action: Usually initiated by the system/customer or raised by an agent in another department. This step rarely requires any effort on the part of the back office agent. The key challenges occurring at this step are the lack of data quality at the trigger point, ineffective rules driving failure demand or missing genuine issues.
2) Investigation: Determining the issue and identifying necessary actions. This is where most manual effort (50-70%) is expended, however rules engines and RPA can follow fixed logic reducing required manual effort. For example, when reviewing meter readings, if the advance is within tolerance, then the read is entered, if not, another action is triggered. AI can offer a more nuanced approach, covering more complex scenarios, however with all automated solutions, poor configuration can lead to process failures and incorrect actions being taken. This in turn can lead to increased waste, impacting cost and CSAT.
3) Action: Executing the required actions (20-40% of effort). Once the required actions are determined, the execution is usually quite straightforward and can be executed using RPA. Changes in system layout or processes can render pre-programmed actions redundant however, leading to increased process fallout, or worse, processes being completed incorrectly, driving rework and impacting CSAT and compliance.
4) Administration: Adding notes/amending records (10-20% of effort). Standard notes can be added via RPA whilst more complex scenarios may require AI/complex RPA. This step is as vulnerable to system changes as previous steps, particularly for more “intelligent” notes which take data from multiple system locations. Maintaining data integrity is also a key consideration in this step.
What causes RPA to lose its effectiveness over time?
Industries like utilities and financial services do not operate in a static environment. Regulations evolve, customer behaviour shifts and maintenance updates can mean systems and processes change too. Here are a few examples of how these changes can impact RPA efficacy:
Policy Changes
Since 2023 Ofgem have assessed and provided new guidance on the Safe and Reasonably Practicable installation and use of prepayment meters. This has not only led to a reduction of meter mode changes from credit to prepayment but has caused an increase in the reverse. Energy suppliers who have failed to pivot quickly and adapt existing automations are being impacted with under-utilised Credit to Prepay automations and high manual effort in processing Prepay to Credit requests, driving high operational costs.
Behavioural Changes
In 2018 around 10m customers changed their energy tariff to get a better deal. In 2022 the number was down to 1.5m and it’s only now starting to climb. In 2018 it was a good idea to automate the change of tariff process, in 2022 the benefit of doing so is significantly less.
Customers aiming to save money may well have taken different steps to do so in the absence of enticing offers by switching supplier, for example calling or emailing for energy efficiency advice or making applications for social tariffs/discounts. Adapting to address changes in customer behaviour is essential to minimise technical debt whilst repurposing to mitigate demand spikes elsewhere.
Process Changes
Systems regularly go through changes as part of maintenance or capability releases. These changes can often have unseen or unintended consequences, impacting established automated processes. For some RPA processes, changing the location of a single data field can completely derail a process and drive process fallout, adding cost into businesses. Change management and business readiness are not always lined up to manage this correctly and, in many cases RPA deliveries are Ops owned and bypass embedded IT change management processes.
System Migration
Integrated/external legacy automations are often overlooked during migration. In cases where automations are developed with operations or “grey IT”, the likelihood of automations being left out of migration scope is even more common. These automations are rarely documented and are subject to key person dependencies, putting them at risk of having no ownership or knowledge in the case of employee turnover. Post-migration typically results in high volumes of unanticipated work that is resourced, or more critically, key system actions failing with work items not being triggered, meaning suppliers have no way of knowing something is broken until a customer contacts them.
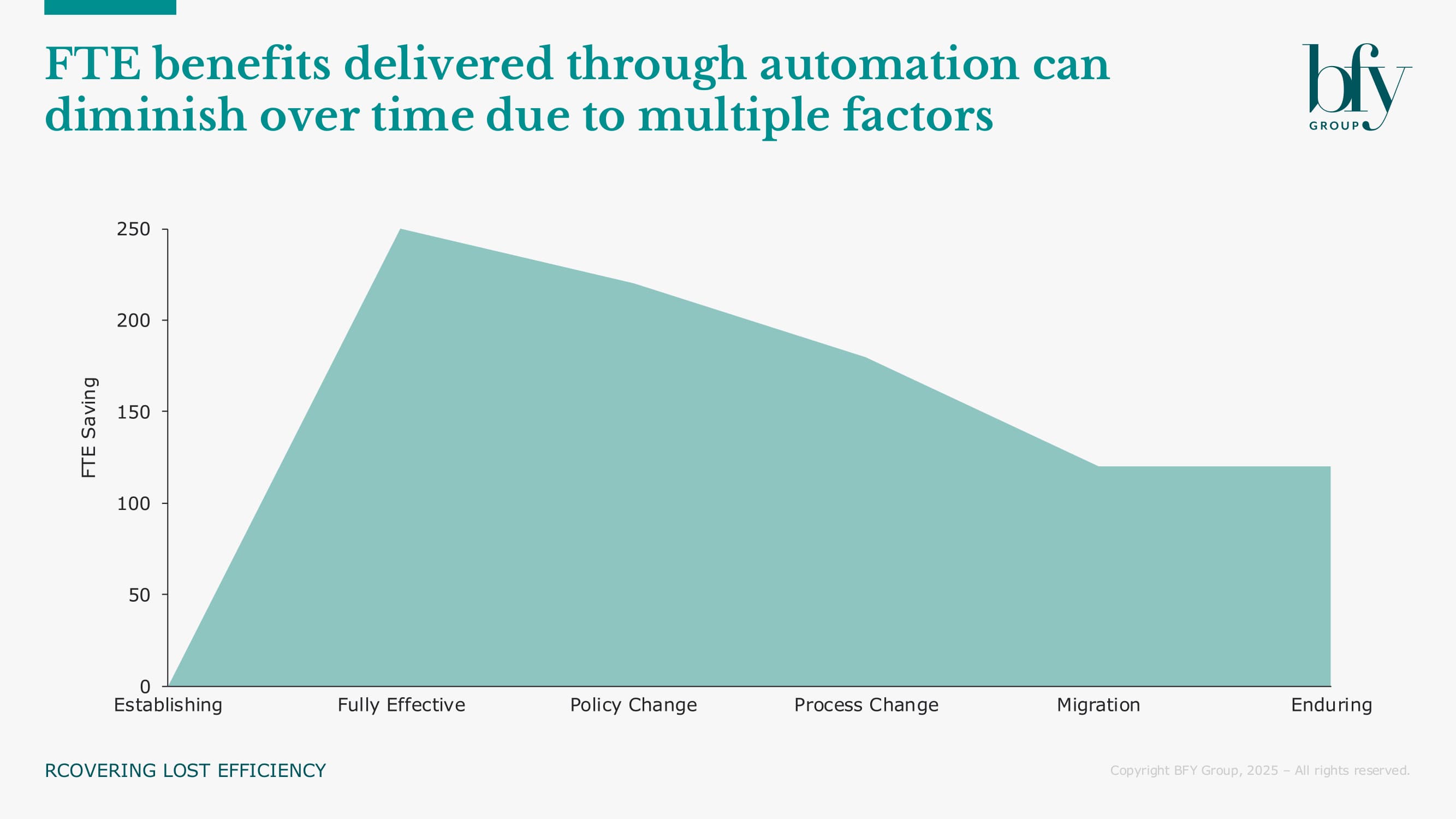
How can automation be revitalised within your business?
If you are a utilities leader and you’ve been impacted by some of these issues, there are four key areas you can focus on to get the most from your automation and redeem any efficiencies you’ve lost:
- Recover lost efficiencies by identifying areas of increased automation fallout and prioritising the highest effort first based on overall volume and effort required. Mapping these processes against existing automations and updating these will bring your processes back on track.
- Review your end-to-end demand against your automation catalogue. If you have high volume, low complexity processes that have no automations, these are the processes to target. If you have active automations aligned to processes that now have little volume/effort, you may consider removing these processes and re-investing these existing RPA licenses and bots on higher value-add activity.
- If you have migrated, completing a new demand analysis is a sure-fire way of identifying the right processes to address. It’s likely some previously automated processes will no longer be automated, and your new system may automate some processes that were previously manual. Establishing a new base line will help you decide which automations to decommission and where you should focus to reduce the most manual effort.
- Ensure that your key processes, automated or not, are mapped and catalogued and are built into your business change and readiness processes. Before a change is released (or even considered), associated processes should be reviewed to inform the business case of any change – if you’re already automating 95% of a particular process, is the IT change justified from a cost/benefit perspective?
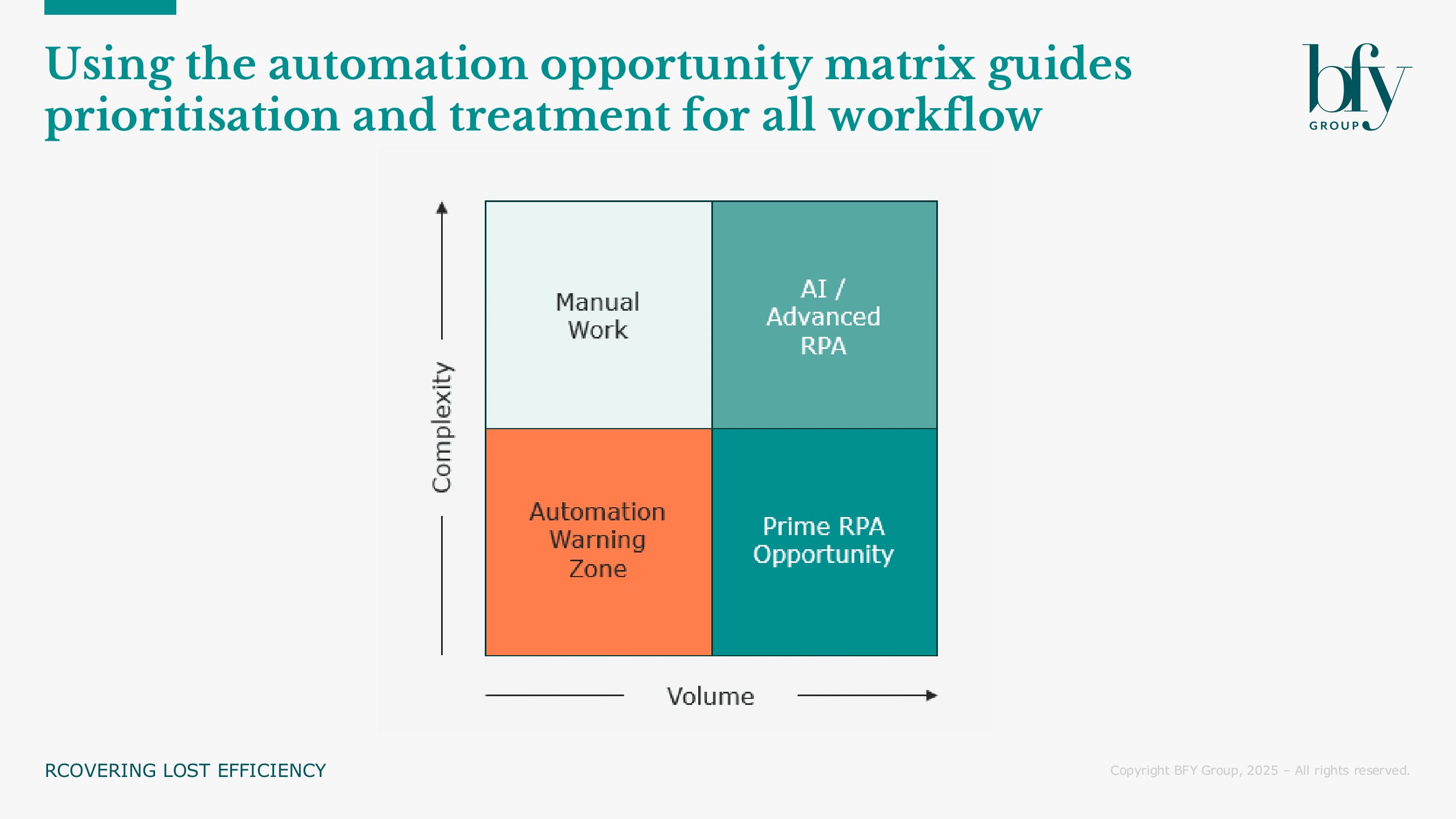
Automation technologies like RPA are now more advanced and capable than ever, but to truly realise their potential, leaders must treat automation as a dynamic asset, not a one-off implementation. The operational and market landscape is always shifting, and your automation strategy must evolve with it.
For utilities, this means regularly reassessing where automation is adding value, where it’s faltering, and where new opportunities are emerging. The good news? Much of the groundwork is already there — it’s a matter of reclaiming, refocusing, and reinvesting.
At BFY, we specialise in helping UK utility businesses do exactly that. Our team brings deep operational, transformational, and automation leadership experience — working shoulder-to-shoulder with clients to recover lost efficiencies and build future-proof back office operations.
Contact Drew Jackson to discuss how BFY can help you refocus your automation strategy and unlock greater value.
Drew Jackson
Manager
Drew partners with our clients to solve complex operational problems and deliver Lean Transformation activity.
View Profile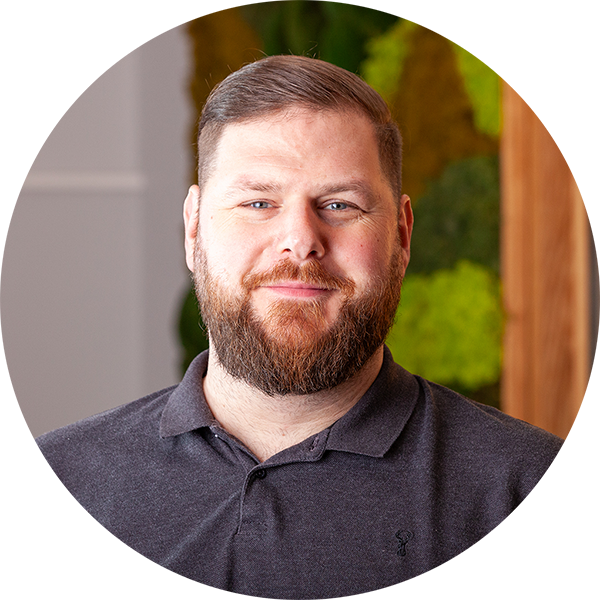